Improving Productivity in Any Plastic Forming Process
Within the current dynamic manufacturing landscape, achieving effectiveness in production processes is more important than ever. Injection molding of plastics service has risen as a dominant method for producing high-quality plastic parts with accuracy and efficiency. As industries range from automotive to the consumer goods sector increasingly depend on this technique, understanding how to maximize efficiency in the molding process is a key focus for manufacturers.
The effectiveness of a plastic injection molding service is not just about the machinery used; it requires refining every aspect of the process, including choosing materials to mold design and cycle times. By utilizing best practices and using advanced technologies, businesses can reduce waste, improve turnaround times, and enhance product quality. This article will explore essential strategies for maximizing efficiency in your plastic injection molding operations, ensuring that you remain competitive in your market.
Comprehending Plastic Injectable Molding
Plastic injection molding represents a fabrication process which utilizes molten polymer material injected into a form to generate accurate and detailed parts. This method is commonly used in various industries because of its capability to generate high volumes of duplicate products with outstanding precision. The procedure starts with deciding on the suitable plastic resin based on the needed characteristics of the completed item, including durability, adaptability, and heat tolerance.
Once the substance is determined, it is heated to the point that it turns into a fluid, and that that is subsequently injected into a carefully designed form. The configuration of the mold is crucial, since it determines the design and characteristics of the final component. After the liquid plastic fills the mold cavity, it hardens and solidifies, allowing the production of complex patterns and features that are often difficult to produce with other manufacturing processes. This efficiency in producing complex forms renders polymer injection molding a popular option for various practices.
Furthermore, the scalability of polymer injectable molding significantly enhances its effectiveness. Once a form is manufactured, it can be used repeatedly to generate thousands upon thousands or possibly millions of identical parts. This repetitive aspect of the process cuts total manufacturing costs and duration. Industries including automotive, retail products, and electronics increasingly rely on polymer injectable forming solutions to meet their large-scale demands while ensuring consistent standards and minimizing waste.
Optimizing Fabrication Techniques
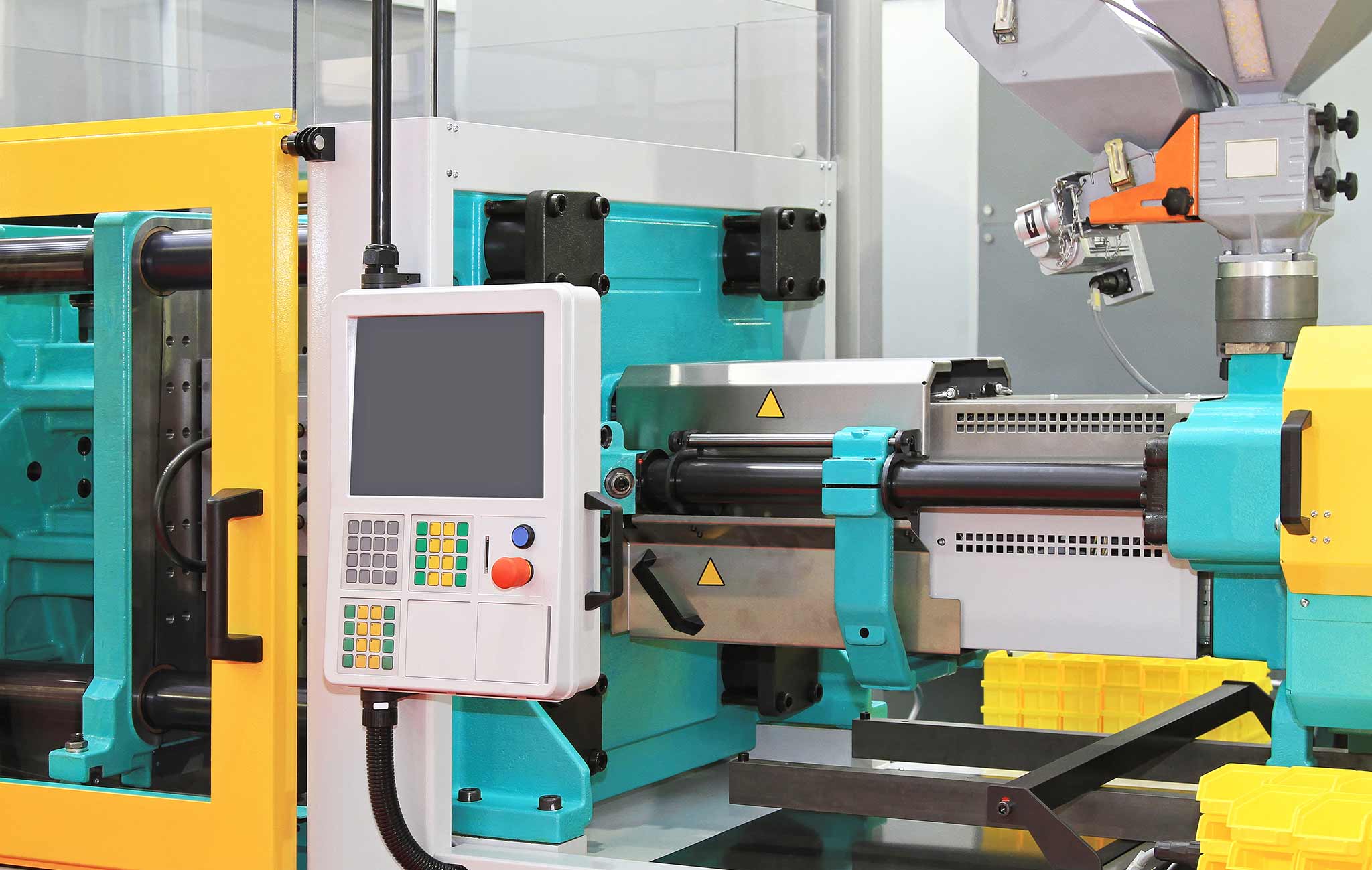
To boost the efficiency of your polymer molded casting operation, it is important to enhance the manufacturing methods used in the manufacturing process. One of the primary actions to implement is the upgrading of cast design. Spending resources in designing premium molds can significantly decrease processing times and increase the durability of the molds. Cutting-edge methods such as material flow analysis and 3D modeling can help in crafting molds that facilitate enhanced material flow and consistent cooling, finally leading to reduced flaws and enhanced output rates.
Another key technique is the adoption of procedure oversight and robotics. By employing modern software and tools, manufacturers can closely observe various factors during the casting procedure, such as thermal levels, tension, and cycle time. This monitoring allows for real-time modifications, lessening inconsistencies and boosting uniformity. Automation can also optimize operations by reducing human work and boosting consistency in manufacturing, which contributes to improved quality products and enhanced efficiency.
Lastly, employee training and participation play a crucial role in enhancing fabrication processes. Delivering your team with thorough training on the newest technologies and top practices in plastic molded molding can lead to increased productivity levels. Engaging employees in solution-finding and procedure enhancement initiatives fosters a climate of continuous improvement. When skilled personnel are enabled to detect and address waste, the total performance of the plastic molded casting operation will thrive greatly, leading to elevated yield and minimized business costs.
Quality Assurance and Upkeep Techniques
Implementing strong quality control measures is crucial in the plastic molding service industry to ensure that the final products meet the required specifications and standards. Regular examination of molds and materials can help identify any discrepancies promptly in the process. Utilizing techniques such as statistical process control can aid in tracking production variations, making sure that the molds operate within the defined parameters. Ensuring uniformity in raw material quality further enhances the dependability of the output, minimizing defects and waste.
Maintenance strategies play a vital role in maximizing efficiency in plastic injection molding. Scheduled preventive maintenance on machinery prevents unexpected breakdowns and prolongs the life of molds, which is important for maintaining production schedules. It is also important to keep all equipment adjusted and in peak working condition. Training employees on proper operating techniques and maintenance routines fosters a culture of quality and reduces human error.
Incorporating input loops into the production process can significantly enhance quality control. By actively seeking input from quality assessments and employee experiences, companies can consistently improve their techniques and address any persistent issues. Implementing real-time monitoring systems allows for swift identification of defects, enabling quick adjustments that preserve both time and resources. Ultimately, a proactive approach to quality control and maintenance not only improves product quality but also enhances total operational efficiency.